- Robotics facts and figures
- Robots in agriculture pick apples, check nutrients, and pack produce
- Robots in healthcare cut tumours, draw blood, and reduce infections
- Robots in retail assist customers, replenish products, and report hazards
- Robots in manufacturing paint vehicles, sort items, and gather tools
- Robots in construction lay bricks, create complex forms, and print bridges
For many of us, robots used to conjure up images of humanoids in sci-fi movies, and we thought them to be kind of creepy. But now that they have become so ubiquitous, this is no longer the case. More and more companies are embracing the robotics revolution, introducing robots to not only automate repetitive, manual processes, but many much more complicated tasks as well. In fact, a third of all the work worldwide is already done by a robot, device, or algorithm. This number is expected to increase in the next couple of years. The latest robotics industry statistics show that robots are slowly but surely becoming an increasingly important part of our lives.
Robotics facts and figures
In 2025, no less than 47 per cent of all tasks and activities will be automated, whether by a robot, another type of device, or a smart algorithm. According to the World Economic Forum Future of Jobs Report 2020, by 2025, 85 million jobs may be displaced by the shift in labour between humans and machines. And according to the International Federation of Robotics, global sales of robotic services are forecast to surpass $55 billion by 2023. The worldwide robotics sector comprises over 500 companies developing products and services. These range from conventional industrial robots and cobots to stationary professional services (agricultural and medical applications), mobile services (construction, professional cleaning, and underwater applications), and automated guided vehicles (AGVs) for transportation on assembly lines or in logistics.
Demands for more speed and efficiency, improved workplace productivity, enhanced safety standards, and increased human-robot collaboration are all important factors driving the worldwide production of robotic units. Between 2017 and 2020, the number of industrial robots installed across industries worldwide exceeded 3 million. And the number of industrial robots sold in 2020 alone was 465,000, bringing the total number of robotic units in use worldwide in that same year to a whopping 12 million.
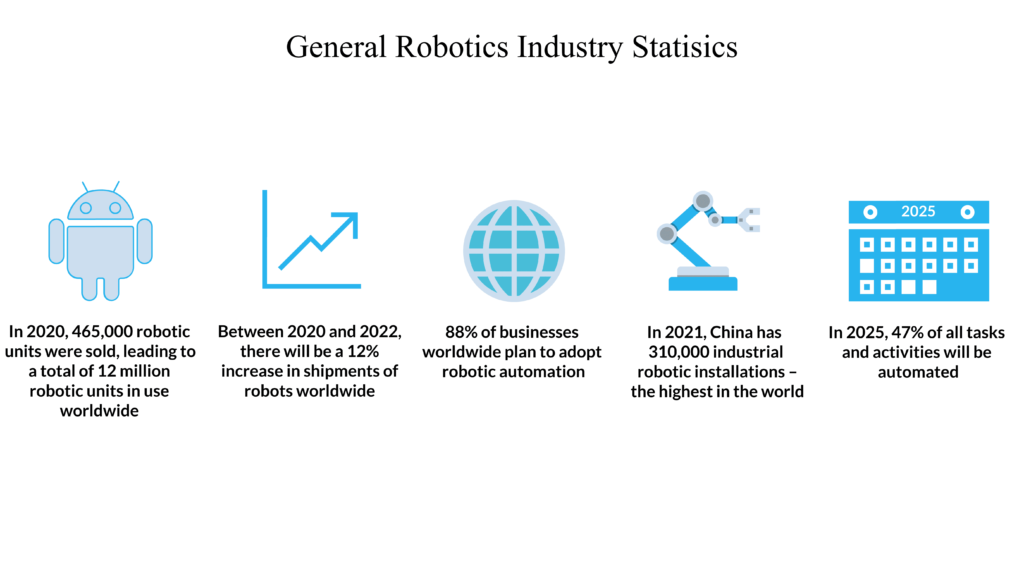
The top trends in industrial robots in 2021, according to the International Federation of Robots, include robots that work in smart factories, such as those on assembly lines in traditional automobile production, and where we’ll see much more networked interaction of autonomous guided vehicles and robots – or autonomous mobile robots – in the future. Other robots that are among the top trends are those that ensure the security of supply chains by offering increased productivity and flexibility. Robots that are able to master complex tasks and learn new ones – accomplished by AI software, combined with vision and other sensing systems – are also among the top trends in industrial robotics. Then there’s robots that reduce carbon footprint, like the ones specifically designed to be energy efficient in order to reduce the production sector’s energy usage. And last but not least, the manufacturing industries that have only recently started implementing robotics, such as the food and beverage industries, textiles, and wood products, are now also part of the top trends.
Robots in agriculture pick apples, check nutrients, and pack produce
Across the globe, pressing challenges like climate change, growing demand for food, and rising labour costs are ushering in a new era of machine modernisation in agriculture. In recent years, more and more companies have invested in autonomous robots and drones than ever before to improve efficiency and free labourers from monotonous, backbreaking work. Machines now milk cows, harvest crops, and package produce more efficiently than humans can. Drones with cameras provide crop information and autonomous systems take care of the weeds, using high-powered laser technology to eliminate pests without damaging surrounding plants or disrupting the soil.
Meet Eve, the Australian apple-picking robot
Year after year, trillions of pieces of fruit are picked by hand. But as farmers continue to struggle with labour shortages, leading to high levels of waste and lost profits, many are considering automating the picking process. At an apple orchard in Goulburn Valley, Australia, some apples will be picked by a robot named Eve this season. The owners of the orchard have partnered with Ripe Robotics to deploy a picking robot with a single suction arm to better position the orchard as an early adopter.
Alex Turnbull, one of the owners of the orchard, says, “We have the robot here all season from late January to May, picking the Gala, Granny Smith, Modi and Pink varieties. If the engineers are also interested in using the robots for pear picking, we will conduct a trial with our Williams pears. We are very excited about the flexibility of this solution and hope to implement it in the long term.”
Eve uses a soft suction system to pick fruit off the tree. It then puts the fruit into a bin and even places the bins at the end of the row. Eve is equipped with artificial intelligence and connects to the cloud. This makes it possible to track the robot’s progress from any location. The Ripe Robotics team has tested its picking robot in various apple, orange, and plum orchards and is planning to introduce a small commercial fleet this year.
Robots Grover and Ada grow crops using hydroponics
Agricultural technology startup Iron Ox believes robots can grow produce more sustainably and wants to do his piece to help make the global agriculture sector carbon negative. The startup secured $53 million in a funding round led by Bill Gates’ Breakthrough Energy Ventures. CEO Brandon Alexander, who spent his childhood summers picking cotton, peanuts, and potatoes at his grandparent’s farm in Texas, now has a degree in robotics “precisely to escape farm work” and to have a bigger impact on agriculture. Alexander explains: “To really eliminate waste, to really get to that next level of sustainability and impact, we have to rethink the entire growth process.”
At Iron Ox’s California-based greenhouse, robots Grover and Ada currently grow strawberries and basil using hydroponics. In the future, Iron Ox wants to grow parsley, tomatoes and cilantro as well. The robots are integrated with a hydroponics system, which consumes 90 per cent less water than traditional farms. The system makes use of artificial intelligence to ensure the plants get all the nutrients, water, and light they need to thrive. The self-driving robot Grover moves pallets of basil to the dosing station, where Ada, a robotic arm equipped with sensors, checks the water for the ingredients needed for healthy growth.
Should the plant need any extra attention, customised nutrient doses are automatically delivered to the plants. The robots ensure that the farm uses water sparingly and produces less waste. By continuously collecting data from the crops, the AI learns exactly what the plants need, which reduces the greenhouse’s environmental impact and improves its yield.
AI-powered picking and packing robots assist farmers
One of the solutions to assist farmers with farm work as COVID-19 restrictions limit the inflow of seasonal labour is robotics technology. Australian startup LYRO Robotics has successfully deployed its picking and packing robots at the Sunnyspot Packhouse avocado facility in Queensland. According to LYRO Robotics managing director and co-founder Dr Jürgen Leitner, the company’s robots can help solve this problem. “The future of robotics is bright, specifically in agriculture where there are a lot of dirty, dull and dangerous jobs – which we usually refer to as 3Ds in robotics,” Dr Leitner said. “Another big advantage of robots is that they can work day or night, don’t need breaks, can work long hours and automate repetitive tasks.”
The picking and packing robots combine machine learning with computer vision and robotic grasping. This enables the robots to see an avocado coming down the line, decide on how to pick up the fruit correctly, and neatly place it into the cardboard box. The robots are also able to sort mangos by ‘blush’. In the mango industry, for instance, a box of mangos with 50 per cent blush generates more revenue in the export market. Dr Leitner and his team have spent many years researching machine learning, robotic vision, and robotic grasping, and to see their hard work coming to fruition is very exciting and rewarding. Dr Leitner says: “The LYRO Machine Intelligence is a deep learning AI software system that integrates the brain, the eyes and the hands, enabling any robot to pick and pack any item, even if it has not seen it before.”
Robots in healthcare cut tumours, draw blood, and reduce infections
Robots have also made significant contributions to healthcare. In fact, between 2016 and 2021, more than 38,000 robotics units were ordered for the global healthcare industry. The pandemic has been especially good for robotics. We’ve seen a surge in the implementation of disinfectant robots, telehealth robots, surgical robots, bots doing health checks at schools, and many others.
CyberKnife ‘cuts out’ tumours with targeted radiation
Invented by Stanford neurosurgeons, the CyberKnife robotic radiosurgery system has been used for decades to treat thousands of patients around the world. With the precision of a knife – and without using an actual blade – CyberKnife’s robotic arms deliver targeted radiation to ‘cut out’ cancerous tumours. With its real-time tumour tracking capabilities, and using 6D motion-sensing technology, CyberKnife enables surgeons to treat only the affected areas while saving healthy tissue.
The CyberKnife system pinpoints the location of the tumour and adjusts its position accordingly. Then, a linear accelerator, which delivers the external beam of radiation, is mounted on the robot that will move around the patient’s body. The high-tech system can adapt to the patient’s movements – like slight muscle contractions or breathing – which could lead to the tumour shifting. The CyberKnife, bending around the patient’s body, keeps tracking the cancerous cells while the radiation beams, from thousands of angles, remain focused on the target with a margin of less than a millimetre.
Veebot takes your blood sample with extreme precision
Developed by a California-based startup and combining the latest in robotics and imaging technology, the Veebot robot was designed specifically for blood drawing. The patient’s arm is inserted into an inflatable cuff. Next, the arm is illuminated by an infrared light and the robot’s camera takes images which are compared with a model of an arm’s veins. Then, ultrasound confirms whether the selected vein will enable a successful blood draw. The robotic arm then aligns itself with the vein and inserts the needle.
The entire process takes less than a minute and is approximately 83 per cent accurate – which is faster and more efficient than a human phlebotomist, even in complex cases. The only thing a human clinician will still need to do is attach the test tube. A fully integrated device, which would include a module to handle samples and a centrifuge-based blood analyser, could be used at bedsides, emergency rooms, ambulances, clinics, and doctors’ offices. The Veebot – and other, similar blood drawing robot systems – can help clinicians get blood samples quickly, safely, and reliably, and will help prevent unnecessary pain and complications from multiple attempts to insert a needle. In the future, blood drawing robots could also be used during procedures like placing arterial lines, central venous access, IV catheterisation, and dialysis.
The Xenex LightStrike robot reduces hospital-acquired infections
Many hospital patients contract hospital acquired infections (HAIs) like C. diff (Clostridium difficile) and MRSA (methicillin-resistant Staphylococcus aureus), and some don’t survive infections like these. Manufactured by Xenex Disinfection Services, a world leader in UV light disinfection for hospitals, the LightStrike robot enables healthcare facilities to significantly reduce the devastating effects of these hospital-acquired infections. The LightStrike robots, which are already being used in hundreds of hospitals around the world, are approximately 91 centimetres tall and look a little like Star Wars’ R2-D2. Using pulsed, high intensity, broad spectrum UV light technology – “a kind of light that doesn’t occur naturally on earth”, according to Xenex spokeswoman Melinda Hart – to disinfect every conceivable surface, the robot is lethal to microorganisms without causing damage to expensive equipment or materials.
The intense UV light produced by these robots inflicts cellular damage to microorganisms and viruses, including the SARS-CoV-2 virus, rendering them incapable of reproduction or mutation. The robot’s disinfection cycles are fast, allowing healthcare centres to disinfect surgical suites in less than 20 minutes, and a patient room in under 10 minutes. University researchers and healthcare facilities have published more than 40 peer-reviewed studies validating the efficacy of the LightStrike robot technology.
Robots in retail assist customers, replenish products, and report hazards
Retail robots are on the rise. In fact, it’s estimated that, by 2025, over 150,000 robots will have been deployed in shops across the world. Experts predict that the need for contactless service will likely accelerate the implementation of robots in the retail sector. Retail robots can assist customers, replenish products, replace cashiers, and carry out stocktaking.
The LoweBot helps shoppers find items
The autonomous retail service ‘LoweBot’, at omni-channel home improvement company Lowe’s, has been assisting customers ever since it was first unveiled a few years ago. The unassuming robot, a 152-centimetre-tall NAVii machine, was developed through a partnership between Lowe’s Innovation Labs and Silicon Valley tech company Fellow Robots. The robot helps customers with simple questions, giving employees more time to focus on personalised customer service.
It uses a 3D scanner for human body frame detection, and engages with customers through speech recognition and a screen that displays detailed product information. The LoweBot greets customers, asks if they need any help, and navigates itself through store aisles without bumping into obstacles. LoweBots can either point out the location of a product or accompany the customer to the product’s location. The LoweBot also scans inventory shelves, remembers inventory details, and captures real-time data, which will generate insights that can be used to inform business decisions.
Marty the Robot reports spills and other hazards to employees
Marty the Robot is a slow-moving retail service robot, as tall as the tallest grocery store shelf, with big, cartoonish eyes. Using laser sensing and cameras, Marty roams the supermarket and alerts customers to problems such as spills and trip hazards. When it detects a hazard, the robot stops, changes its operating lights from blue to yellow, and says “caution, hazard detected,” in English and Spanish. It then contacts an employee via the public announcement system of the store. The robot is powered by rechargeable lithium batteries and uses its integrated cameras to navigate around the store, making sure it doesn’t bump into store displays or customers.
Marty wears a description on its body that reads: “Marty is an autonomous robot that uses image capturing technology to report spills, debris, and other potential hazards to store employees to improve your shopping experience.” Marty is also equipped to check products and identify missing labels or incorrect pricing. The data collected by Marty helps stores with inventory management and scheduling product delivery. Many customers like seeing Marty around and enjoy taking selfies with the robot. Others, however, think Marty’s presence is a little unsettling. Throughout 2019, giant, aisle-patrolling Martys have been deployed in over 500 supermarkets in the United States.
Robots in manufacturing paint vehicles, sort items, and gather their own tools
More and more manufacturers are embracing robotics and automation to provide solutions to production challenges. Some benefits of robotics in manufacturing include greater overall flexibility, lower labour costs, the ability to quickly increase or decrease production, higher throughput and quality, less waste, and more economical use of floor space. And to give you an idea of the vastness of the industrial robotics market, the Japanese Fanuc corporation – the largest maker of industrial robots in the world with customers in sectors like warehousing, automotive, pharmaceutical, and aerospace – recently announced it had built its 750,000th industrial robot.
The EcoRP E043i robot paints vehicle bodies
EcoRP E043i, made by global mechanical and plant engineering firm Dürr Systems AG, is a 3rd-generation paint robot that is used to paint vehicle bodies. It is fitted with seven axes, multiple sensors, and has incredible flexibility and mobility. Its design allows it to reach areas that are difficult to access, such as vehicle interiors. And thanks to its new, optimised control system, the robot can move the atomiser around the surface while maintaining a constant distance and speed, ensuring a consistent layer of paint. More and more leading vehicle manufacturing companies are making use of these types of advanced machines. “The new EcoRP E043i from our third robot generation has been equipped with a seventh rotary axis. This significantly increases flexibility and versatility”, says Hans Schumacher, president and CEO of Dürr Systems AG.
The EcoRP robots can be installed on bottom or top-mounted rails and placed anywhere – whether on the wall, on the floor, or the ceiling – and at various angles, too. The advanced system’s improved drive technology, cooling, and motion capabilities lead to up to 30 per cent in energy savings. According to the Durr website, “the EcoScreen 3D OnSite software designs the paint path and spray patterns for the complete painting station. The robot control system transfers the data for the motion sequence and the painting. Teaching of the robot is only necessary when dealing with difficult parts for fine-tuning.”
The TossingBot can sort items and toss them in a container
Google recently unveiled its TossingBot robot arm. The robot can pick random objects from a box and toss them into a container that is well beyond its physical reach. The robot can easily be trained on how to handle any new objects and can pick, sort, and toss up to 500 items per hour. Applications of the TossingBot could include pick-and-place tasks in warehouses, on assembly lines, and in logistics centres. Tossing items instead of physically moving them has various advantages, such as increasing throughput on assembly lines and reducing the number of human staff members needed to distribute items to different locations.
Andy Zang, one of the student engineers working on the development of the TossingBot, explains: “The robot has learned to pick up arbitrary objects from a cluttered bin and place them into a box that is located outside the maximum reach range of the robot. Overhead cameras track where the object lands and the system learns from experience and improves itself over time.” Zang continues: “The bot uses deep learning algorithms to associate the visual appearance of an object with how to grasp it and how to throw it. It’s also an incredibly general system – for example, you could train it to throw toy blocks and it’ll still perform reasonably well with bananas.”
HelMo mobile assembly line robot autonomously navigates its surroundings
Assembly line robots are extremely accurate and fast. They provide flexible automation, can be redeployed for process changes, and are able to work with a host of different parts. They can be programmed to operate autonomously or be guided by a robotic vision system. Assembly line robots are used to put parts together, insert pins and screws, and perform a myriad of other tasks. They are able to handle parts that are too intricate, too delicate, or simply too small for humans to handle. To make assembly robot operations even more precise and improve assembly quality, these machines can be fitted with force sensors to provide feedback about, for instance, whether more or less pressure is required.
The HelMo robot, developed by Swiss technology group Stäubli International AG, is a high-performance mobile robot system that works and navigates through its surroundings fully autonomously. Once trained, this collaborative robot can handle almost any manual task on all kinds of assembly lines, including direct human-robot collaboration. Using three integrated laser scanners, with which it permanently monitors its environment, HelMo independently navigates to its own workstation and correctly positions itself using three orientation points. The robot then connects itself to sockets for compressed air and electricity, gathers its own tools and materials, and gets to work.
The robot is fitted with an automatic tool changing system so that it can tend to multiple machines. HelMo autonomously selects the appropriate tool to complete a task and then moves on to the next job. The robot is safe enough to work alongside human workers, as it reduces speed or stops completely when it’s in close proximity to a person. By communicating with each other as well as with a higher-level ERP system, multiple HelMos can be networked to serve complete production lines.
Robots in construction lay bricks, create complex concrete forms, and print steel bridges
The construction industry is one of the most labour-intensive industries in the world. As a result of the transition to Industry 4.0, worldwide labour shortages, as well as social distancing measures during the pandemic, the industry has been increasingly forced to implement advanced technology like construction robotics. Some of the most notable construction robots are the Hadrian X bricklaying robot and the Odico formwork robot that creates complex moulds for concrete casting.
The Hadrian X bricklaying robot lays 1.000 bricks per hourHadrian X, the world’s first mobile robotic bricklaying machine developed by FBR in Australia, made headlines when it laid 1,000 bricks in an hour. As human bricklayers typically lay 300-500 bricks per day, it’s easy to see why this bricklaying robot is impressive. The robot uses specially designed, interlocking blocks that are 12 times larger than traditional bricks. While traditional mortar takes 1-2 days to dry, the mortar that has been specifically developed for use by the robot dries within 45 minutes. Hadrian X can currently lay 200 of these special bricks in an hour, using a 30-metre boom which delivers the bricks to the layhead. The robot can also grind, cut, mill, and route the bricks to fit. The robot’s telescopic arm enables it to lay bricks around corners and build curved walls. Hadrian X builds structures from a 3D CAD model, producing far less waste than traditional construction methods. In the near future, the bricklaying robot will be able to build a typical home within two days.
Odico’s mobile robot creates complex concrete moulds on-site
Creating concrete moulds is often a detailed, painstaking, and very labour-intensive undertaking. Danish company Odico Formwork Robotics has now developed robots that use innovative ways to generate moulds for concrete casting. The robots replace manual labour and enable concrete manufacturers to cut costs for formwork by almost 90 per cent. Odico’s robots use the ‘hot wire cutting’ technique, which enables them to produce complex concrete moulds that would take humans a long time to create. And Odico’s ‘Factory On The Fly’ system, a robotic system that fits inside a standard container and can be shipped to building sites, is used to custom-create building elements with complex shapes, including formwork, reinforcement, insulation, and even tiles.
The system is developed to generate significant savings in terms of time, labour costs, and sourcing and shipping custom-made products from specialists. Odico has already completed various high-profile construction projects, such as the Opus Dubai building designed by Zaha Hadid Architects. Odico chief technology officer Asbjørn Søndergaard says: “Factory On The Fly enables on-site, parametric production of advanced formwork and custom building components. It is operated from a standard iPad, allowing for simple interaction and operation by non-specialist personnel. It bypasses the current technocracy of robot manufacturing and replaces it with a straightforward user experience, the simplicity of which is on a par with using conventional tablet apps.”
The MX3D robot prints stainless steel bridges
A 12 metre-long stainless steel pedestrian bridge, 3D printed by Dutch robotics company MX3D, was recently installed across one of the oldest and most famous canals in the centre of Amsterdam, the Oudezijds Achterburgwal. The six-axis robots that MX3D adapted to print the bridge can rotate their arms along six different planes of movement, building up structures by depositing layer upon layer of small amounts of steel. The robots can create much larger structures by moving across them as they print, unlike traditional 3D printers. The MX3D robots first printed a load-bearing structure to support their own weight as they printed the bridge.
“The basics of the technology is pretty simple. We’re using an industrial robot that is usually used in assembly lines in the car industry. We have combined this with a welding machine and our own software to have it 3D print in metal”, Joris Laarman, designer and cofounder of MX3D explains. “In the end this project will result in a really big library of algorithms and scripts that in the future we can use for all kinds of geometries. I think robots will be really important for construction in the future. By printing with robots you are not bound to the limitations in size of what 3D printers usually have, so we can theoretically print endlessly big. The next goal would be to build a bridge on site in mid-air as the robot moves along the structure as it builds it.”
The bridge also functions as a living laboratory for data scientists. The smart sensor network that monitors the bridge’s health in real time has been developed by a group of IoT specialists, engineers, and mathematicians. The sensors collect structural measurements like vibration, strain, and displacement. They also measure environmental factors like temperature and air quality, enabling engineers to ‘teach’ the bridge, in a way, to understand how many people use it and what happens when people use it. Machine learning algorithms enable the bridge to interpret the environment and respond intelligently. A digital twin of the bridge receives this data to inform future designs of printed metal structures.
In closing
While the adoption of robots across various industries is happening at an increasing pace, there are still many other dirty, repetitive, delicate, and dangerous tasks that could be done by robots, which would result in improved employee health, safer work environments, and increased job satisfaction. Robots produce incredibly consistent, accurate, and high quality work without needing breaks or holidays. Robots also help solve challenges around hazardous environments and back-breaking labour. In the future, human-robot collaboration will increasingly complement the use of traditional robotics. Modern robots are also expected to play a significant role in reducing our carbon footprint and can lead to increased revenue.