- Artificially intelligent trash-sorters are becoming an increasingly common sight
- ZenRobotics’ trash-sorting robot can learn to identify new kinds of materials
- The Clarke recycling robot can identify and pick up milk, juice, and food cartons from a pile of trash
- Is the technology advanced enough to completely replace humans?
Sorting trash is one of the most dangerous occupations, and employees in this industry worry about high injury and fatality rates. A recent study by environmental, occupational safety, and community benefits experts reveals that recycling workers are two times more likely to suffer work-related injuries than other employees. For instance, between 2011 and 2013, seventeen of these workers in the US lost their lives on the job. Unsafe working conditions around heavy machinery and exposure to hazards such as toxic chemicals, hypodermic needles, and animal carcasses are some of the main reasons behind these unfavourable statistics. “Recycling is the right thing to do, but we have to do it the right way,” says Mary Vogel, the executive director of the National Council for Occupational Safety and Health. “That means educating and empowering recycling workers, and using proven prevention strategies which we know will reduce exposure to hazardous conditions.”
Artificially intelligent trash-sorters are becoming an increasingly common sight
One of these strategies involves incorporating robots into the workplace and letting them take care of the dirty, dangerous parts of the job. And thanks to recent advancements in artificial intelligence, trash-sorting robots are becoming an increasingly common sight in recycling plants across the US. Using cameras and sophisticated deep learning algorithms programmed to recognise specific objects, the robots can identify cans, plastic containers, glass, or any other kind of recyclable material in a pile of trash within seconds, pick them up using suction cups or large tongs, and deposit them into the appropriate bins. Not only are they just as accurate as humans in performing this task, they’re also up to two times faster, making them a very powerful tool in future recycling efforts. “It’s still very early days,” explains John Standish, the technical director of the Association of Plastic Recyclers, a trade group in Washington, D.C. “But I’m very, very optimistic for the future.”
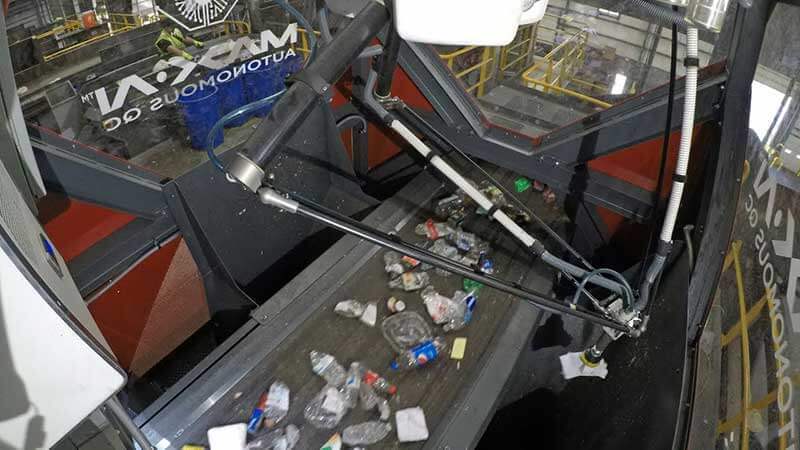
ZenRobotics’ trash-sorting robot can learn to identify new kinds of materials
The Finnish company ZenRobotics was the first to bring a trash-sorting robot to the market. Unveiled in 2011, the robot uses a combination of artificial intelligence, machine learning, and computer vision to pick up and sort items from moving conveyor belts. The company was also the first to link its recycling stations into a neural network, which allowed the AI to select and sort items from the belt with fantastic accuracy by learning from the data supplied by metal sensors, 3D laser cameras, and spectroscopic cameras. Today, the company’s robots are used in 10 different countries.
We throw away unimaginable amounts of trash every year, but a lot of it could actually be recycled, especially metals. Furthermore, as mining is extremely harmful to the environment, recycling metals can provide a much greener alternative that can not only reduce our environmental impact, but also help us satisfy the demand for materials that are in limited supply. “There is always a demand for raw materials, but the recycled ones have to now be much cleaner and better sorted — closer to mined raw materials,” says ZenRobotics’ CEO, Timo Taalas. Using scanners, the ZenRobotics system measures each object’s characteristics, such as surface structure, shape, and material composition. It even has the ability to learn to identify new kinds of materials. All you have to do is feed it 200 samples and you’re ready to go. This learning ability provides companies with much-needed flexibility and makes the adoption of the technology much easier. “If you build a traditional sorting plant, you make a huge investment but it’s a fixed configuration. In this business, the legislation changes, the material values change – our system can be easily reconfigured,” explains Taalas.
Apple has also recently announced that it’s started using robots to take apart iPhones in California and the Netherlands. Compared to traditional methods like shredding, robots have proven much more effective at preserving resources, according to the company. Currently used to take apart water-damaged units, the robots are capable of extracting up to 190 kg of aluminium, 80 kg of copper, and smaller amounts of platinum, gold, silver, and tin out of every 10,000 units they process.
The Clarke recycling robot can identify and pick up milk, juice, and food cartons from a pile of trash
AMP Robotics recently joined forces with Alpine Waste & Recycling and the Carton Council to build a recycling robot named Clarke that can separate food and beverage cartons from the rest of the trash. “The fundamental platform that we’ve created was a system to sort pretty much all the commodities that are in a recycling facility today,” says AMP Robotics founder Mantanya Horowitz. “Whether it’s cardboard, No. 1 plastics, No. 2 plastics, or cartons — cartons just ended up being a great place for us to start.”
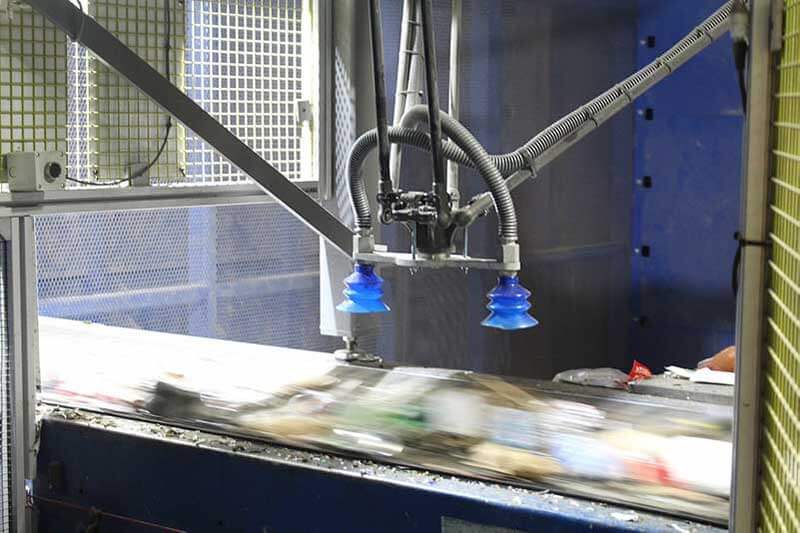
Built from an off-the-shelf robot that’s been in use by other industries for more than twenty years, Clarke uses artificial intelligence and a visible-light camera to identify milk, juice, and food cartons from a pile of trash, and then uses suction cups attached to its robotic arms to pick them up. Clarke is capable of identifying and grabbing 60 items per minute with 90 per cent accuracy. It also does it 50 per cent faster than a human worker. And since Clarke is driven by artificial intelligence, it can only get better with time as it processes more information. “Even though this first system is picking cartons, it’s actually watching and learning from all the other commodities that it’s seeing as well,” adds Horowitz. “That’s what’s really exciting. The more systems that we have out there, the better they’re going to be.”
The company hopes it will be able to further improve Clarke’s sorting abilities by adding more granularity. “Right now we can say, ‘That’s a No. 1 plastic’ but we want to be able to say ‘That’s a Pepsi bottle, that’s a Gatorade bottle’ and give recycling facilities even finer resolution on what’s going through [their lines],” explains Horowitz.
Is the technology advanced enough to completely replace humans?
Many people have raised concerns that trash-sorting robots could take jobs away from human workers, but that may not necessarily be the case. As impressive as they are, trash-sorting robots aren’t flawless. Many experts believe that the technology isn’t advanced enough to completely replace humans, and that some sorting will always have to be done manually, simply because some materials don’t mix well. “If you mix wet waste organics with paper-based waste, you get a mess and paper is devalued if it is dirty,” says Rob van Dalen of Bollegraaf Recycling Solutions. Another issue that’s preventing wider adoption is that recycling robots are still too expensive, with a two-armed ZenRobotics system currently going for €700,000 – €800,000.
Despite some concerns about their impact on human workers, trash-sorting robots provide numerous benefits. They can significantly increase efficiency and decrease costs in recycling plants. They could also help create additional jobs in a wide variety of firms that reuse raw materials, such as paper mills or plastic recyclers. And last but not least, they could have a very positive impact on the environment by reducing the amount of trash that ends up in our landfills and oceans.